Use and maintenance of rubber rollers
Author: hongyuanTime:
1. The pressure between the rubber rollers is too heavy. The pressure between the rubber rollers is heavy, which will increase the friction between the rubber rollers, causing the rubber rollers to heat up, aggravating the squeeze and expansion between the rubber rollers, and accelerating the aging and aging of the rubber rollers. Deformation will speed up the emulsification process of ink and water, which is not conducive to the transfer of ink.
The solution is: the pressure between the rubber rollers should be basically the same as the pressure on the contact surface. My experience is to use a 1500 thread, 3cm wide plug piece to insert between the rubber rollers, and you can feel a certain tightness.
After scrubbing, wipe it again with a clean cloth and install the rubber roller on the machine for next use.
2. Treatment of crystallization on the surface of the rubber roller. Surface crystallization seals the capillary pores on the surface of the rubber roller, which will cause the rubber roller to lose its ability to absorb ink, resulting in uniform ink transfer and prone to emulsification of the ink.
The solution is: remove the rubber roller from the machine, lay it flat on a shelf, stick kerosene and pumice powder on a cloth, wipe the surface of the rubber roller evenly, wipe off the crystallized layer on the surface of the rubber roller, and reveal the original The rubber color of the rubber roller, then use car wash water or gasoline to clean the kerosene and pumice powder remaining on the rubber roller, reinstall and adjust the pressure of the rubber roller.
3. Maintenance of the bearings on the rubber roller. During the high-speed operation of the machine, the wear of the bearing on the rubber roller is very obvious, especially if the operator pays attention to the maintenance cloth of the bearing at ordinary times, the wear will be even more severe. After the bearing of the rubber roller is damaged to a certain extent, the rubber roller will jump, friction and squeeze, shortening the service life of the rubber roller. And it will cause the printed products to have “ink and water streaks”. Therefore, operators are required to take down the rubber rollers every week, grease the bearings, and replace the bearings that are severely worn and rotate poorly to ensure the normal use of the rubber rollers.
4. The impact of stacking rubber rollers on the workshop environment. In production environments with hot and humid weather and flying dust from the surroundings, the high-speed operation of the machine causes the surface temperature of the rubber rollers to continue to rise. The rubber rollers heat and expand, increasing the amount of rubber. The friction of the roller will shorten the service life of the rubber roller.
Therefore, in factories with good conditions, offset printing plug-ins require the installation of air conditioners to keep the workshop neat and clean so that the machines can operate in a good environment. Only in a good workshop environment can high-quality products be produced.
① Neoprene rubber: suitable for making various soft printing rollers, gravure printing rollers, etc. Rubber roller forming can be done by molding, film wrapping, winding or extrusion forming. Due to the poor storage stability of the rubber, care should be taken to avoid parking in direct sunlight during the manufacturing process. At the same time, the temperature conditions under which the rubber material is parked must be controlled.
② Nitrile rubber: used to manufacture printing rubber rollers, food industry rubber rollers, textile printing and dyeing rubber rollers, soft rubber rollers in contact with solvents, etc. Nitrile rubber has poor ozone resistance, so operations in environments with high ozone concentrations should be avoided during processing. When nitrile rubber and polyvinyl chloride are used together, a rubber compound with better ozone resistance and weather resistance can be obtained.
③ Polyurethane rubber: It has outstanding tensile strength, wear resistance and crack resistance. Polyester polyurethane rubber has good resistance to various solvents. In addition, continuous exposure of the rubber to high temperatures and humidity will also adversely affect performance. For polyurethane rubber rollers used under high speed and high pressure, the focus is to improve the problem of dynamic roll off and cracks.
④ Silicone rubber: It has heat resistance of 200-250 degrees and good chemical resistance. Its main disadvantage is low tensile strength. Typical uses of silicone rubber rollers include heat setting of fabrics, heat setting embossing and calendering of plastics, and fixing of copy machines, etc. The molded silicone rubber roller is formed by film wrapping. Due to its low strength, the operation must be careful.
⑤ Chlorosulfonated polyethylene; has high toughness and elasticity. Wear resistance, heat resistance up to 150 degrees, good resistance to various chemicals and oils, and excellent insulation. It can be manufactured by various methods except casting. The rubber material should be protected from sunlight during the production process.
⑥ Ethylene-propylene rubber: It can be used under high temperature conditions of 150 degrees. It has excellent resistance to chemicals and polar solvents, but is not resistant to hydrocarbon solvents and oils. It can be used to make extrusion rubber rollers, conveyor rubber rollers, and contact rubber rollers. Printing rollers containing inks based on acetone and ester solvents. The roll can be rolled or extruded. Please be careful to avoid contact with oil and hydrocarbon solvents during process operations.
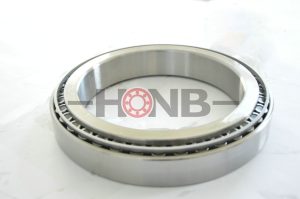
We have rich experience in precision bearing manufacturing and are ranked NO.1 in China and NO.3 all over the world.
We can tailor the overall solution for the use of precision bearings.
HONB– Accountability & Innovation
Products
- YRT rotary table bearing
- YRTS rotary table bearing (high speed series)
- YRTM with integral angular measuring system series
- ZKLDF axial angular contact ball bearing series
- RA series crossed roller bearing
- SX series crossed roller bearing
- CRBH series crossed roller bearing
- RE series crossed roller bearing
- RU series crossed roller bearing
- RB series crossed roller bearing
- XR/JXR series crossed taper roller bearing
- Crossed roller bearing
Contact Us
✉️ bearing20@hyzcgroup.com
📞 +86 15236685001