Types and causes of bearing surface roughness defects
Author: hongyuanTime:
Crossed spiral marks on the surface
The reason for such traces is mainly due to the poor straightness of the grinding wheel bus and the existence of concave and convex phenomenon. The pitch of these spirals is related to the workpiece table speed, the size of the workpiece speed, and also to the non-parallelism of the grinding wheel axis line and the table guide.
► The main reason for the formation of spiral lines
1. poor dressing of the grinding wheel, the edges are not chamfered, and no coolant is used for dressing.
2. too much lubricating oil for table guide, resulting in table floating.
3. poor precision of the machine tool.
4. Excessive grinding pressure, etc.
►Spiral line formation of specific reasons
1. poor rigidity of the V-shaped guideway, when the grinding wheel is deflected during grinding, only the edge of the grinding wheel is in contact with the working surface.
2. unstable table reversing speed and low precision when dressing the noisy wheel, which makes the dressing of a certain edge of the grinding wheel slightly less.
3. poor rigidity of the workpiece itself.
4. the grinding wheel has broken too flaking sand particles and iron chips under workpiece grinding accumulated on the surface of the grinding wheel, for which the dressed grinding wheel should be flushed or brushed clean with cooling water.
5. The grinding wheel is not well dressed, with local projections, etc.
The surface appears fish scale
The main reason for the reproduction of fish scale marks on the surface is that the cutting edge of the grinding wheel is not sharp enough, and the phenomenon of “gnawing” occurs during grinding, when the vibration is large enough to cause the workpiece.
The specific reasons for the appearance of fish scale marks on the surface are.
1. garbage and oil on the surface of the grinding wheel.
2. the grinding wheel is not rounded.
3. the grinding wheel becomes dull. Insufficient dressing sharpness.
4. the diamond fastening frame is not firm, the diamond shakes or the diamond quality is not sharp.
5. Uneven hardness of the grinding wheel, etc.
Pulling of the working surface
The main reason for the surface reproduction of bristle marks is caused by the abrasive grains caught between the workpiece and the grinding wheel after the coarse-grained abrasive grains are dislodged.
► The specific reasons for the surface of the workpiece to be stretched during grinding are
1. traces left over from coarse grinding and not ground off during fine grinding.
2. unclean filtration of coarse abrasive particles and micro abrasive particles in the coolant.
3. coarse-grained grinding wheels are easily dislodged when they are just dressed.
4. the material toughness is valid or the grinding wheel is too soft.
5. improper matching of abrasive grain toughness and workpiece material toughness, etc.
Workpiece surface with straight waveform traces
We will cut a cross section of the workpiece with vertical axis and magnify it, and we can see that its periphery is close to a sine wave. Make its center along the axis line without rotation translation, the sine wave around the trajectory is the waveform column surface, also known as polygon.
The cause of the straight waveform is the movement of the grinding wheel relative to the workpiece or the periodic change of the pressure of the grinding wheel on the workpiece, which causes vibration. This vibration may be forced vibration or self-excited vibration, so there is often more than one straight wave frequency on the workpiece.
► The specific reasons for generating straight waveform traces are.
1. excessive grinding wheel spindle clearance.
2. too high hardness of the grinding wheel.
3. poor static balance of the grinding wheel or dulling of the grinding wheel
4. the workpiece speed is too high.
5. too large transverse her knife
6. abrasive wheel spindle bearing wear, with excessive clearance, resulting in radial runout.
7. grinding wheel clamping mechanism or table “crawling”, etc.
Reproduction of burn marks on the surface of the workpiece
There are several types of burns on the surface of the workpiece during the grinding process: one is a dark black patch along the grinding wheel processing direction; the other is a line or intermittent line.
► The surface of the workpiece is burned during the grinding process for the following reasons.
1. the grinding wheel is too hard or grit is too fine organization is too dense.
2. excessive feed, insufficient supply of cutting fluid and poor heat dissipation conditions.
3. the workpiece speed is too low and the grinding wheel speed is too fast
4. excessive oscillation of the grinding wheel and burns due to constant changes in grinding depth.
5. untimely dressing or poor dressing of the grinding wheel.
6. sharp diamond and poor dressing of the grinding wheel.
7. the workpiece is burned too deeply during rough grinding and the amount left for fine grinding is too small and not ground off.
8. Insufficient workpiece clamping force or suction force, and the workpiece has stagnation phenomenon under the grinding force, etc.
So how do you know if the workpiece surface is burned during grinding? This can be checked by regular pickling.
After pickling the workpiece, when the surface is wet, it should be visually inspected immediately under the diffuse light, and the normal surface is uniformly dark gray. If it is a software point, it presents a cloud-like dark black spots, and the perimeter of the variable whole; if decarburization, it presents gray or dark black spots; if the grinding process cracks, the cracks are cracked, such as burns, one is the surface along the direction of the grinding wheel processing presents dark black patches, and the second is the presentation of lines or intermittent lines like.
If the above burn phenomenon occurs in the grinding process, we must analyze the cause in time and take effective measures to solve the problem and eliminate the batch burn.
Surface roughness does not meet the requirements
The surface roughness of bearing parts have standards and process requirements, but in the grinding and super-finishing process, for various reasons, often fail to meet the specified requirements.
The main reasons for the surface roughness of the workpiece not meeting the requirements are.
1. the grinding speed is too low, the feed speed is too fast, the feed is too large, and the grinding time without feed is too short.
2. the workpiece speed is too high or the vibration of the workpiece shaft and grinding wheel shaft is too high
3. the grinding wheel grit is too coarse or too soft
4. the grinding wheel dressing speed is too fast or the dressing mechanism clearance is too large
5. the diamond for dressing the grinding wheel is not sharp or of poor quality.
6. the quality of the oil stone for superfinishing is not good and the installation position is not correct.
7. the quality of kerosene for superfinishing is not up to the requirement.
8. superfinishing time is too short, etc.
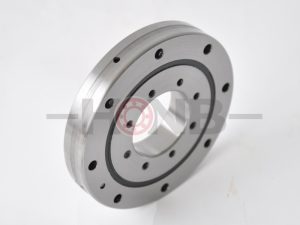
We have rich experience on precision bearing manufacturing and are ranked NO.1 in China and NO.3 all over the world.
We can tailor the overall solution for the use of precision bearings.
HONB– Accountability & Innovation
Products
- YRT rotary table bearing
- YRTS rotary table bearing (high speed series)
- YRTM with integral angular measuring system series
- ZKLDF axial angular contact ball bearing series
- RA series crossed roller bearing
- SX series crossed roller bearing
- CRBH series crossed roller bearing
- RE series crossed roller bearing
- RU series crossed roller bearing
- RB series crossed roller bearing
- XR/JXR series crossed taper roller bearing
- Crossed roller bearing
Contact Us
✉️ bearing20@hyzcgroup.com
📞 +86 15236685001