Precautions for installation and debugging of machine tool parts
Author: hongyuanTime:
Precautions for installation and debugging of mechanical parts of CNC machine tools:
1. Precautions for installation and debugging of spindle bearings
(1) Installation and commissioning of a single bearing
When assembling, try to make the eccentricity of the spindle positioning inner hole and the spindle shaft diameter and the eccentricity of the bearing inner ring and the raceway as close as possible, and make them in the opposite direction, so that the eccentricity after assembly can be reduced.
(2) Installation and debugging of two bearings
When installing the two supported spindle bearings, the eccentricity direction of the front and rear two supporting bearings should be the same, and the eccentricity should be properly selected. The accuracy of the front bearing should be one grade higher than that of the rear bearing to minimize the eccentricity of the front end positioning surface of the assembled main shaft components. When disassembling the main shaft bearing for repairing the machine tool, because the original manufacturer has adjusted the eccentric position of the bearing, it is necessary to mark the position in the circumferential direction before disassembly, so as to ensure that the original relative position of the bearing and the main shaft remains unchanged after reassembly, and reduce the damage to the main shaft parts. influences.
When assembling bearings with interference fit, hot or cold installation should be used for installation. Do not knock them violently, so as not to damage the bearings during the installation process and affect the performance of the machine tool.
2. Precautions for installation and debugging of ball screw nut pair
The ball screw nut pair is only used to bear axial load. Radial force and bending moment will cause adverse loads such as additional surface contact stress on the ball screw pair, which may cause permanent damage to the screw. Therefore, when the ball screw nut pair is installed on the machine tool, attention should be paid to:
(1) The ball nut should move within the effective stroke, and limit stops must be arranged at both ends of the stroke to prevent the nut from overtraveling and detaching from the screw shaft, causing the ball to fall off.
(2) Due to the high transmission efficiency of the ball screw nut pair, it cannot be self-locked. When it is used for vertical transmission, if the weight of the component is not balanced, it must prevent the reverse transmission caused by the self-weight of the component after the transmission stops or the motor loses power. , The method of preventing reverse transmission is available: worm gear transmission, electric brake, etc.
(3) The axis of the lead screw must be parallel to the axis of the matching guide rail, and the center of the bearing seat at both ends of the machine tool and the center of the nut seat must be in line with three points.
(4) When the ball screw nut pair is installed on the machine tool, do not remove the nut from the screw shaft. If it must be removed, use an auxiliary sleeve, otherwise the ball may fall off during loading and unloading.
(5) When the nut is installed in the mounting hole of the nut seat, it is necessary to avoid impact and eccentricity.
(6) In order to prevent chips from entering and wearing the ball screw nut pair, protective devices such as wrinkle protection covers, spiral steel belt protection sleeves, etc. can be installed to completely protect the screw shaft. In addition, when there is a lot of floating dust, dust-proof rings can be added at both ends of the screw nut.
3. Precautions for installation and debugging of linear rolling guide rail
(1) Handle with care during installation to avoid bumps affecting the linear accuracy of the guide rail.
(2) It is not allowed to detach the slider from the guide rail or push it back after exceeding the stroke. If the slider needs to be removed due to installation difficulties, guide rails are required.
(3) When the linear rolling guides are used in pairs, the main and auxiliary guide rails are divided into main and auxiliary guide rails. First, install the main guide rail. As a benchmark, find and install the auxiliary guide rail pair. Alignment refers to the parallelism and flatness of the two guide rail pairs. Finally, tighten the fastening bolts of the slider one by one.
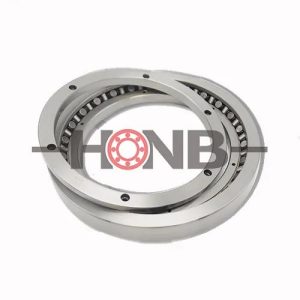
We have rich experience on precision bearing manufacturing and are ranked NO.1 in China and NO.3 all over the world.
We can tailor the overall solution for the use of precision bearings.
HONB– Accountability & Innovation
Previous Page:Vibration and temperature inspection of bearings
Products
- YRT rotary table bearing
- YRTS rotary table bearing (high speed series)
- YRTM with integral angular measuring system series
- ZKLDF axial angular contact ball bearing series
- RA series crossed roller bearing
- SX series crossed roller bearing
- CRBH series crossed roller bearing
- RE series crossed roller bearing
- RU series crossed roller bearing
- RB series crossed roller bearing
- XR/JXR series crossed taper roller bearing
- Crossed roller bearing
Contact Us
✉️ bearing20@hyzcgroup.com
📞 +86 15236685001