Mechanical seal selection introduction-II
Author: hongyuanTime:
The use of multiple smaller springs creates a more even load pressure on the seal face and therefore has a greater susceptibility to clogging. For many highly corrosive applications, the most common design is a metal bellows seal. The bellows are welded from a series of metal discs to form a bellows seal that prevents leakage. The adoption of this device can make the sealing pressure between the sealing surfaces more uniform, and there is no need to add secondary seals on the sealing surfaces, so naturally no corrosion and wear will occur.
In order to ensure that the sealing surfaces always cooperate with each other, the spring plays a role of constant adjustment between the mechanical seal and the moving main shaft. When an elastomeric seal is used between the rotating surface and the spindle, the elastomer moves back and forth on the spindle. This repeated friction action will wear away the anti-corrosion material on the main shaft, lose the oxide film protection layer of the main shaft, and eventually form wear grooves on the friction surface of the main shaft, causing liquid to leak from the grooves and increasing the necessary maintenance workload Or even replace the spindle. In order to solve this problem, a replaceable shaft sleeve is generally installed in the stuffing box. However, the only permanent solution to the corrosion wear problem is to remove the dynamic seal inside it. Most major seal manufacturers now produce non-corrosive wear seals to prevent corrosion and wear of pump parts. Balanced and unbalanced seal The balance of the mechanical seal has a great influence on the sealing pressure of the contact surface. This sealing pressure depends on the effective cross section of the seal itself and the pressure inside the stuffing box. The section on the opposite side of the rotating surface of the unbalanced seal is completely exposed to the pressure range of the stuffing box, which will cause a high sealing pressure between the sealing surfaces, which will increase the working temperature and accelerate the wear rate. Under high temperature working conditions or when the liquid is highly corrosive and abrasive, the service life of the mechanical seal will be greatly reduced. Balancing the mechanical seal can reduce the sealing pressure and prolong the service life of the seal.
The outer seal mainly has the following five advantages:
1) Easy to install;
2) The cost is relatively low;
3) It can be continuously monitored and cleaned;
4) Suitable for very small stuffing boxes that cannot be sealed inside;
5) Due to its location close to the bearing, it has less influence on the difficulty of the main shaft deviation.
Its main disadvantage is that centrifugal force will throw solid particles from under the seal to the contact surface of the seal. Therefore, this type of seal is mainly suitable for clean and non-abrasive liquids. In recent years, split seals have become another important additional feature in outer seals. The separate seal is a complete assembly, installed between the stuffing box and the bearing sleeve. With this design, it is not necessary to disassemble the liquid pump every time the seal needs to be replaced. Such seals are being developed in conjunction with other design criteria discussed. Since this design allows for easy seal replacement, it is important to resist the temptation to simply replace the seal without further investigation into the root cause of the failure. Cartridge seal The cartridge seal is an all-in-one sealing device, which includes all sealing elements, glands and bushings. Since this type of seal does not require any strict installation measures, the installation procedure is greatly simplified, and the sealing surface and sealing elastomer are well protected to prevent accidental damage. It also means less time for seal repair and replacement.
It has a cartridge-type sealing device with all functions, which can simplify the installation procedure and protect the internal components from accidental damage. Almost all types of cartridge seals are commercially available, thus reducing the risk factor in use and also saving maintenance time inherent in the use of conventional seals. Double seal and liquid barrier device adopts the seal of double sealing surface instead of single seal to have a higher degree of leak-proof characteristics. Most of these double seals are used in highly volatile, toxic, carcinogenic, dangerous and poorly lubricated liquids.
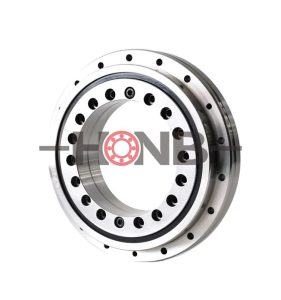
We have rich experience on precision bearing manufacturing and are ranked NO.1 in China and NO.3 all over the world.
We can tailor the overall solution for the use of precision bearings.
HONB– Accountability & Innovation
Previous Page:Summary of mechanical seal selection introduction
Products
- YRT rotary table bearing
- YRTS rotary table bearing (high speed series)
- YRTM with integral angular measuring system series
- ZKLDF axial angular contact ball bearing series
- RA series crossed roller bearing
- SX series crossed roller bearing
- CRBH series crossed roller bearing
- RE series crossed roller bearing
- RU series crossed roller bearing
- RB series crossed roller bearing
- XR/JXR series crossed taper roller bearing
- Crossed roller bearing
Contact Us
✉️ bearing20@hyzcgroup.com
📞 +86 15236685001