Whether the spherical bearing is installed well or not will affect the accuracy, life and performance of the spherical bearing. Therefore, please fully study the installation of spherical plain bearings, that is, please follow the steps including the following items to install spherical plain bearings. 1) Cleaning spherical bearings and related parts For grease-lubricated spherical bearings with oil seals or dust covers on both sides, there is no need to clean the sealed ring spherical bearings before installation. 2) Check the size and finishing of relevant parts 3) Installation method The installation of spherical plain bearings should be based on the structure, size and matching properties of the spherical plain bearing components. The pressure should be directly applied to the end face of the tight-fitting ring, and the pressure must not be transmitted through the rolling elements. The following methods are generally used for the installation of spherical plain bearings: A. Press fit When the inner ring of the spherical bearing has a tight fit with the shaft, and the outer ring has a loose fit with the spherical bearing seat hole, a press can be used to press the spherical bearing on the shaft first, and then the shaft and the spherical bearing are installed into the spherical bearing seat hole. , when pressing, place an assembly sleeve (copper or mild steel) made of soft metal material on the end face of the inner ring of the spherical bearing. The inner diameter of the assembly sleeve should be slightly larger than the journal diameter, and the outer diameter should be larger than the inner diameter of the spherical bearing. The ring rib is slightly smaller to avoid pressing on the cage. When the outer ring of the spherical bearing fits tightly with the spherical bearing seat hole, and the inner ring and the shaft fit loosely, the spherical plain bearing can be pressed into the spherical bearing seat hole first. At this time, the outer diameter of the assembly sleeve should be slightly smaller than the diameter of the seat hole. If the spherical bearing ring is a tight fit with the shaft and seat hole, the inner ring and outer ring of the installation must be pressed into the shaft and seat hole at the same time. The structure of the assembly casing should be able to simultaneously press the end faces of the inner and outer rings of the spherical bearing. .
B. Heating and matching The installation method of heating the spherical bearing or spherical bearing seat and using thermal expansion to convert the tight fit into a loose fit is a common and labor-saving installation method. This method is suitable for the installation of spherical bearings with large interference. Before hot installation, put the ring of the spherical bearing or separable spherical bearing into the oil tank and heat it evenly to 80-100°C, then remove it from the oil and install it on the shaft as soon as possible. In order to prevent the end face of the inner ring and the shaft shoulder from loosening after cooling, the spherical bearing can be tightened axially after cooling. When the outer ring of the spherical bearing is tightly matched with the spherical bearing seat made of light metal, the hot-fitting method of heating the spherical bearing seat can avoid scratches on the mating surface. When using an oil tank to heat a spherical bearing, there should be a grid at a certain distance from the bottom of the tank, or a hook is used to hang the spherical bearing. The spherical bearing cannot be placed on the bottom of the tank to prevent impurities from entering the spherical bearing or uneven heating in the oil tank. A thermometer is necessary to strictly control the oil temperature not to exceed 100°C to prevent tempering effects and reduce the hardness of the ferrule.
C. Installation of tapered bore spherical bearings The tapered bore bearing can be directly installed on the tapered journal, or on the tapered surface of the adapter sleeve and withdrawal sleeve. The tightness of the fit can be measured by the reduction in radial clearance of the spherical bearing. Therefore, before installation, The radial clearance of the spherical bearing should be measured. During the installation process, the clearance should be measured frequently to achieve the required clearance reduction. During installation, locking nuts are generally used for installation, and heating installation methods can also be used.
D. Installation of thrust spherical bearings The fit between the thrust bearing ring and the shaft is generally a transition fit, and the fit between the seat ring and the spherical bearing seat hole is generally a clearance fit. Therefore, this kind of spherical bearing is easier to install. The central axis of the two-way thrust spherical bearing should be fixed on the shaft. , to prevent rotation relative to the axis. The installation method of spherical bearings is generally when the shaft rotates. Therefore, the fit between the inner ring and the shaft is an interference fit, and the fit between the outer ring of the spherical bearing and the spherical bearing chamber is a clearance fit.
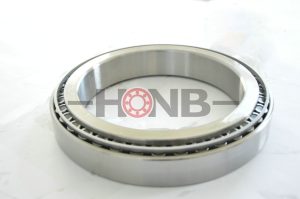
We have rich experience in precision bearing manufacturing and are ranked NO.1 in China and NO.3 all over the world.
We can tailor the overall solution for the use of precision bearings.
HONB– Accountability & Innovation
- YRT rotary table bearing
- YRTS rotary table bearing (high speed series)
- YRTM with integral angular measuring system series
- ZKLDF axial angular contact ball bearing series
- RA series crossed roller bearing
- SX series crossed roller bearing
- CRBH series crossed roller bearing
- RE series crossed roller bearing
- RU series crossed roller bearing
- RB series crossed roller bearing
- XR/JXR series crossed taper roller bearing
- Crossed roller bearing
✉️ bearing20@hyzcgroup.com
📞 +86 15236685001