Introduction to the basic elements of spindle selection
Author: hongyuanTime:
1. The structure and characteristics of the main shaft
Belt-driven spindle; direct-coupled spindle; built-in spindle (electric spindle), double-contact (with HSK, BBT, NBT handle) taper-bore spindle; spindles with the same speed have many different characteristics, and should be selected reasonably, for example: The bearing size, specification and bearing position are different; the rigidity of the spindle has different indicators; the length of the front end of the spindle has different specifications; Knife loosening, etc.);
2. Main axis selection elements
The design of machine tools generally takes the maximum cutting force of the machine tool as the first element. At the same time, the maximum cutting speed, maximum cutting torque, spindle rotation accuracy, machine tool structure requirements, processing materials, cutting conditions and other factors should be considered comprehensively when choosing.
If you are not proficient in the design and calculation of the spindle, you can roughly calculate it from the tool tension force on the spindle sample to ensure that the spindle can withstand the maximum cutting force. Generally, the tool tension force is about two times greater than the maximum axial cutting force that the spindle can withstand.
The commonly used maximum speed during processing is not higher than 80% of the maximum speed provided on the sample.
Selection of pull stud type: steel ball tensioning device is generally selected for the spindle whose speed is below 6000 rpm, and it can also be used for those with small cutting force; four-jaw tensioning device should be used for high-speed spindles above 8000rpm and strong cutting.
Spindle cooling selection: the shaft diameter is less than 70mm, the maximum speed is 8000rpm (discontinuous operation) can not be selected, and the high-precision machining center must be selected. The selection and definition of cooling should be based on the consideration of accuracy, and try not to be based on damage considerations.
Selection of medium spray function: machine tools for processing aluminum alloy, titanium alloy, and stainless steel are recommended, and machine tools for processing small holes and deep holes are recommended.
Selection of air curtain protection function: Generally, it should be selected, especially for machine tools that process graphite materials, plastic materials, and aluminum alloy materials. The compressed air of machine tools that use this function must be dry, otherwise the inside of the spindle will be rusted.
Selection of tool release reverse buckle function: This function can protect the spindle bearing from the impact of tool release force and prolong the service life of the bearing.
For spindles with the same tapered hole specification, spindles with large outer diameters are often equipped with large steel balls or large ceramic ball bearings, which have high rigidity, stable cutting, and can withstand large cutting forces. They are generally used on high-power, powerful cutting machine tools.
When purchasing the main shaft, it is best to ask the supplier to provide the transmission parts and basic installation size requirements at the same time, so as to realize the complete supply and avoid mistakes.
Try to choose the spindle of our company’s standard specifications, the price is relatively low, and the delivery time is short.
3. Precautions for selection and use
Belt drive type: The belt drive type has no gear vibration and noise problems at high speeds, and can be used at higher speeds, but the mandrel is vibrated by lateral forces. At low speeds, the belt transmission efficiency is almost suitable for low-speed heavy cutting. At high speeds, the belt And air friction noise is quite large, when the dmn value exceeds 1000000mm/rpm, other transmission methods should be used.
Built-in type: the most widely used in high-speed cutting, light weight is most suitable for high-speed movement, while the number of parts is small, dynamic balance correction and alignment are easy, and vibration is low.
Motor direct connection type: In order to reduce the vibration caused by the lateral force on the spindle, the motor and the main shaft are connected by a coupling, and the speed can be higher than that of the belt-driven main shaft. to 20000rpm.
Speed: The speed required for high-speed cutting is mainly determined by the material of the workpiece, the material of the cutting tool, and the diameter of the cutting tool. The speed of the high-speed spindle with the BT40 specification is mostly below 15,000 rpm, and the most is 10,000 rpm and 12,000 rpm. The speed of the high-speed spindle with the BT50 specification is mostly below 12,000 rpm, and the most is 1,000 rpm. Applied in the high-speed cutting of light alloy and other materials, the spindle speed is mostly above 20,000rpm. The tool holder specification is usually HSK-A63, and the larger workpiece is processed by HSK-A100.
Horsepower: In the goal of improving the processing efficiency, whether the horsepower of the spindle is sufficient is also our concern. In high-speed cutting, the horsepower of the high-speed spindle is much higher than that of the traditional spindle, but the rigidity of the machine must also be able to match. Otherwise, know how to exert part of the horsepower to cause vibration of the machine structure. In domestic machine tool factories, some machines are directly replaced with high-speed spindles. The main goal is to increase the cutting speed and process light alloys or soft materials. High cutting rates are not required, and relatively small horsepower can be used. Rigidity: Insufficient spindle rigidity will affect machining accuracy, but rigidity exceeding functional requirements will result in reduced spindle bearing life. When the Dmn value is low, fixed position preload can be used. When the temperature rises during high-speed rotation, the preload will be aggravated, and the bearing spacer ring can be used for cooling, which has a good effect on easing the increase of preload. When the Dmn value is high, constant pressure preloading can be used to ensure the preloading value. Grease lubrication can be used when the dmn value is low, and its rigidity value must be lower than that of oil-air lubrication, so as to avoid shortening the life of the spindle due to the temperature rise and accelerated grease deterioration when the preload is too large.
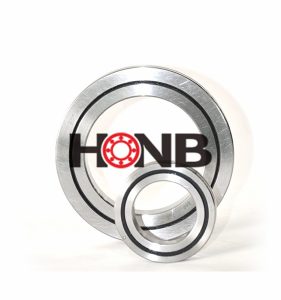
We have rich experience on precision bearing manufacturing and are ranked NO.1 in China and NO.3 all over the world.
We can tailor the overall solution for the use of precision bearings.
HONB– Accountability & Innovation
Products
- YRT rotary table bearing
- YRTS rotary table bearing (high speed series)
- YRTM with integral angular measuring system series
- ZKLDF axial angular contact ball bearing series
- RA series crossed roller bearing
- SX series crossed roller bearing
- CRBH series crossed roller bearing
- RE series crossed roller bearing
- RU series crossed roller bearing
- RB series crossed roller bearing
- XR/JXR series crossed taper roller bearing
- Crossed roller bearing
Contact Us
✉️ bearing20@hyzcgroup.com
📞 +86 15236685001