For more than 100 years, people have used various sealing materials such as packing to continuously reduce the leakage of liquid from the pump housing along the main shaft. Although liquid pumps are used in modern processes, the oldest sealing design, the stuffing box, is still widely used because it has a low initial cost and is familiar to factory workers. However, due to environmental issues, the use of packing seals has gradually become unacceptable, especially for highly corrosive liquids that are common in modern processes. Therefore, in practical applications, mechanical seals are increasingly used instead of packing seals. The seal between the rotating surface and the stationary surface is the most critical factor that determines the sealing performance of the mechanical seal. There are 4 leakage paths that need to be sealed: 1) The passage between sealing surfaces; 2) The passage between the rotating surface and the spindle; 3) The passage between the fixed surface and the gland; 4) The passage between the gland and the stuffing box. The latter two leakage paths are generally statically sealed because there is no relative movement between the two parts. This part of the seal is usually called the third seal, and the sealing material is a gasket or an O-ring that is compatible with the process liquid. In newer seal designs, the secondary seal is stationary, thus avoiding wear and corrosion problems on the spindle. In normal operation of the liquid pump, the pressure between the rotating surface and the stationary surface is maintained in a sealed state by the pressure generated by the liquid in the stuffing box. During startup and shutdown, the pressure in the stuffing box is maintained by the pressure generated by the spring. Most mechanical seal designs use softer materials to make the rotating surface so that it rotates and rubs against the harder stationary surface. For many years, the most common combination utilized a carbon material as a rotating surface, running on a ceramic stationary surface. From this point of view, it is very important that these sealing contact surfaces must be handled carefully and installation instructions strictly followed to ensure that the sealing surfaces are properly protected and correctly seated. Flexibility of sealing: The axial and radial movement of the spindle needs to maintain a certain degree of flexibility with the spring to ensure sealing between the contact surfaces. However, only a certain degree of flexibility is provided. The mechanical condition of the liquid pump and its length-to-diameter ratio (a measure of the ratio of the diameter of the spindle to its extended length, the lower the ratio, the better) play an important role in the reliability of the seal. Sealing flexibility is generally provided by a large main spring and a series of small springs or bellows sealing devices. The traditional seal design used in the chemical industry applies sealing pressure to a rotating surface. This type of seal is called a rotary seal because the spring or bellows seal device rotates with the main shaft. A relatively new design in which a spring or corrugated sealing device is mounted on a stationary surface. In today’s mechanical seals, the above two sealing methods are very commonly used, which allows a certain degree of flexibility in installation. Many mechanical seals designed in the early days used a single large spring arranged around the main shaft, which can provide a strong sealing force for the sealing surface during the starting process of the liquid pump. The sealing function relies on the rotation of the main shaft to tighten the spring roll. The seal designed later uses a series of smaller springs arranged around the main shaft, which can produce a relatively uniform load pressure on the sealing surface. Since smaller springs can be installed in advance, most of these seals are completely isolated from the liquid being pumped. The use of multiple smaller springs can produce a more even load pressure on the sealing surface, so it is more sensitive to clogging. For many corrosive applications, the most common design is a metal bellows seal. The bellows consists of a series of metal discs welded together to create a corrugated seal that prevents leakage. The use of this device can make the sealing pressure between the sealing surfaces more uniform, and there is no need to add a secondary seal on the sealing surface, so naturally there will be no corrosion and wear. In order to ensure that the sealing surfaces always cooperate with each other, the spring plays a constant regulating role between the mechanical seal and the moving spindle. When an elastomer seal is used between the rotating surface and the spindle, the elastomer moves back and forth on the spindle. This repeated friction action will wear away the anti-corrosion material on the spindle, lose the protective oxide film of the spindle, and eventually form wear grooves on the friction surface of the spindle, causing liquid to leak from the grooves and increasing the amount of necessary maintenance work. Or even replace the spindle. In order to solve this problem, a replaceable sleeve is usually installed in the stuffing box. However, the only permanent solution to the problem of corrosive wear is to remove the dynamic seal within it. Most major seal manufacturers now produce non-corrosive wear seals to prevent corrosive wear of liquid pump parts. Balanced and Unbalanced Seals The balance of a mechanical seal has a great influence on the sealing pressure at the contact surface. This sealing pressure depends on the effective cross-section of the seal itself and the pressure inside the stuffing box. The cross-section on the opposite side of the rotating surface of the unbalanced seal is completely exposed to the pressure range of the stuffing box. This situation will generate a high sealing pressure between the sealing surfaces, which will increase the operating temperature and accelerate the wear rate. Under high-temperature working conditions or when the liquid is highly corrosive and frictional, the service life of the mechanical seal will be greatly reduced. Balancing the mechanical seal can reduce the sealing pressure and extend the service life of the seal. The external seal mainly has the following five major benefits: 1) Easy to install; 2) The cost is relatively low; 3) Can be continuously monitored and cleaned; 4) Suitable for very small stuffing boxes that cannot be sealed inside; 5) Due to its location close to the bearing, it has less difficult influence on the spindle deviation. Its main disadvantage is that centrifugal force will throw solid particles from the bottom of the seal to the contact surface of the seal. Therefore, this type of seal is mainly suitable for clean and non-abrasive liquids. In recent years, split seals have become another important additional feature in external seals. The separate seal is a complete assembly installed between the stuffing box and the bearing sleeve. With this design, there is no need to disassemble the liquid pump every time when the seal needs to be replaced. Such seals are being developed in conjunction with other design criteria. Since this design makes it easy to replace the seal, it is important to resist the temptation to just replace the seal without further investigation into the source of the failure. Cartridge seal Cartridge seal is an all-in-one sealing device, which includes all sealing elements, glands and sleeves. Since this type of seal does not require any strict installation measures, the installation procedure is greatly simplified, and the sealing surface and sealing elastomer are well protected to prevent accidental damage. It also means reduced seal repair and replacement time. It has its own fully functional cartridge sealing device, which simplifies the installation process and protects various internal components from accidental damage. Almost all types of cartridge seals are commercially available, thus reducing the risk factors involved in their use and also saving the maintenance time inherent in using ordinary seals. Double sealing and liquid barrier devices use double sealing surfaces instead of a single seal to provide a higher degree of leakage prevention. This type of double seal is mostly used in liquids that are highly volatile, toxic, carcinogenic, dangerous and have poor lubricity.
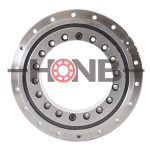
We have rich experience in precision bearing manufacturing and are ranked NO.1 in China and NO.3 all over the world.
We can tailor the overall solution for the use of precision bearings.
HONB– Accountability & Innovation
- YRT rotary table bearing
- YRTS rotary table bearing (high speed series)
- YRTM with integral angular measuring system series
- ZKLDF axial angular contact ball bearing series
- RA series crossed roller bearing
- SX series crossed roller bearing
- CRBH series crossed roller bearing
- RE series crossed roller bearing
- RU series crossed roller bearing
- RB series crossed roller bearing
- XR/JXR series crossed taper roller bearing
- Crossed roller bearing
✉️ bearing20@hyzcgroup.com
📞 +86 15236685001