Home > News > Product Knowledge > Influence of Raw Materials on Forging Microstructure and Properties
Influence of Raw Materials on Forging Microstructure and Properties
Author: hongyuanTime:
The raw materials for forging are ingot, rolled material, extruded material and forged billet. Rolled products, extruded materials and forged billets are semi-finished products formed after ingots are rolled, extruded and forged respectively. For cast ingots, the composition of the furnace charge, the smelting method and the forging process are important links that determine its quality. The rolling, extrusion and forging process is another link that determines the quality of the corresponding semi-finished products.
Before the raw materials enter the forging process, they need to be inspected for size, surface quality, chemical composition, high-magnification structure, low-magnification structure and mechanical properties, and can only be put into production after meeting the technical requirements.
The chemical composition, high-magnification structure, low-magnification structure and mechanical properties of raw materials are the basis to ensure the structure and performance of forgings, while the size and surface quality of raw materials directly affect the process plasticity and forming of forgings. In addition, the forgeability of raw materials and their recrystallization characteristics are the basis for determining forging process parameters.
Therefore, the good quality of raw materials is a prerequisite for ensuring the quality of forgings.
However, the quality inspection of raw materials has certain limitations (such as missed inspections and unrepresentative sampling, etc.), and the inspection methods stipulated by the technical conditions of raw materials cannot expose all quality problems inside the steel, such as: Internal composition and segregation, etc. Therefore, various defects in raw materials will inevitably affect the forming process of forgings and the final quality of forgings.
The influence of raw materials on the structure and performance of forgings mainly includes the following aspects:
1. The influence of chemical composition and impurity elements
In the technical conditions of raw materials, the corresponding composition ranges are stipulated for chemical elements, and there are also certain restrictions on impurity elements such as S, P, Cu, Sn, and Pb. The chemical elements beyond the specified range and the content of impurity elements are too high will have a great impact on the forming and quality of forgings.
S, B, Cu, Sn and other elements tend to form low-melting point phases, making forgings prone to hot embrittlement.
Al content has a certain influence on the essential grain size of alloy structural steel. In order to obtain essential fine-grained steel, the residual aluminum content in the steel needs to be controlled within a certain range (such as: Al acid 0.02~0.04%). If the aluminum content is too small, it will not be able to control the grain growth; the aluminum content Too much, under the condition of forming fibrous structure during press processing, it is easy to create wood grain fracture, tear-like fracture, etc., which will reduce the mechanical properties and performance of forgings.
In 1Cr18Ni9Ti austenitic stainless steel, the more content of Ti, Si, Al and Mo, the more ferrite phase, the easier it is to form surface cracks during forging, and make the parts magnetic.
The eutectic in the raw material has a great influence on the formation of the forging and the quality of the forging. It makes the material easy to overburn and reduce the plasticity index of the material when it is heated before forging. Such as: primary eutectic carbides in ledeburite tool steel, dendritic eutectic compounds in aluminum alloy extruded rods, etc. The coarse β phase in titanium alloy raw materials directly affects the general mechanical properties of forgings.
2. The influence of internal defects of raw materials
Defects such as shrinkage tube residues, subcutaneous air bubbles, severe carbide segregation, and coarse non-metallic inclusions (slag inclusions) inside the raw material can easily cause cracks in forgings.
Defects such as dendritic crystals, severe porosity, non-metallic inclusions, white spots, overturning, oxide film, delamination, segregation bands, and foreign metals in the raw materials can easily cause the performance of forgings to decline. A small amount of non-metallic inclusions also have a greater impact on the life of cold rolls and bearing steel.
3. The influence of surface defects of raw materials
Surface cracks, folds, scars, coarse crystal rings, etc. on the surface of raw materials are likely to cause surface cracks on forgings.
4. The influence of raw material streamline
The rolled material, extruded material and forging blank for forging and die forging all have fibrous structure, so their properties are directional, which is also the basic reason for the directional properties of forgings. The severity of its directionality depends not only on the content of S, P and other impurities in the raw material, but also on the forging ratio of the raw material. Therefore, when choosing a forging scheme for forgings, attention should be paid to the correct distribution of streamlines according to the stress of the parts.
The forgeability and recrystallization characteristics of raw materials also have a great influence on the forming and quality of forgings. Materials with good forgeability have good formability. Generally speaking, carbon steel and alloy structural steel have high process plasticity, low deformation resistance and good forgeability. However, high-alloy and high-temperature alloys have low process plasticity, high deformation resistance, and poor forgeability. The aluminum alloy is in the middle, and all alloys have a certain critical deformation range. When the deformation degree is within this range, the grains are particularly coarse, which reduces the mechanical properties of the forging. This critical deformation range should be avoided during forging.
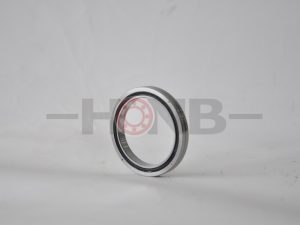
We have rich experience on precision bearing manufacturing and are ranked NO.1 in China and NO.3 all over the world.
We can tailor the overall solution for the use of precision bearings.
HONB– Accountability & Innovation
Previous Page:Types and functions of oil seals
Next Page:Common types of grease
Products
- YRT rotary table bearing
- YRTS rotary table bearing (high speed series)
- YRTM with integral angular measuring system series
- ZKLDF axial angular contact ball bearing series
- RA series crossed roller bearing
- SX series crossed roller bearing
- CRBH series crossed roller bearing
- RE series crossed roller bearing
- RU series crossed roller bearing
- RB series crossed roller bearing
- XR/JXR series crossed taper roller bearing
- Crossed roller bearing
Contact Us
✉️ bearing20@hyzcgroup.com
📞 +86 15236685001