Improper use causes early damage to bearings
Author: hongyuanTime:
When bearings are in use, early damage is a common failure of bearings. Early damage to bearings can also take many forms. For example, improper bearing coordination, improper installation, and improper maintenance will all lead to the possibility of early damage. The editor will share the following aspects of the specific situation. Early damage caused by improper bearings.
1. Damage caused by unqualified size, shape and position accuracy of the workpiece mated with the bearing
If the mating surfaces of the workpiece shaft and the housing hole are not vertical, or the roughness of the bearing positioning surface is unqualified, or the shaft is bent, the axes of the inner and outer rings of the bearing will be skewed to each other and cause the rings and rollers to skew. The local contact stress on the rolling surface increases significantly, resulting in fatigue spalling and early damage.
If the workpiece shell hole is oval or tapered, the ferrule will be deformed and endanger the raceway, causing premature wear and fatigue damage of the raceway. Similarly, if the matching journal geometry between the workpiece shaft and the bearing is incorrect, it will also cause damage to the bearing inner ring raceway. If the shaft diameter is too large, it may cause the inner ring to rupture, as shown in Figure 2; if the housing hole diameter is too large, it will cause the outer ring to loosen and slip, which will intensify the wear of the housing hole and the outer diameter of the outer ring.
2. Bearing damage caused by improper installation and operation methods
The inner component and outer ring of the tapered roller bearing are installed on the shaft and in the shell respectively. During assembly, the ring raceway and rollers can be damaged due to skew, impact or excessive assembly force. This damage can occur even if If it is very small, it will also aggravate the damage of the raceway. If there is a bump on the roller, the bearing will also cause damage to the raceway of the ring after rotation.
During the installation process, if you use the press-in method to assemble the bearing, you must use a special sleeve tool, because directly hitting the ferrule with an iron rod may cause cracks or end face damage in the ferrule, or even cause the inner ring rib to break. . In order to avoid cracks, it is not advisable to directly hit the ferrule with an iron rod during installation, but a copper liner must be added.
When using special sleeve tools to assemble internal components, attention should be paid to the inner and outer diameters of the sleeve to avoid deforming the cage due to the sleeve pressing on the end face of the cage. Severe deformation may cause the rollers to scatter.
If the inner components of the bearing are accidentally dropped to the ground or hit during transportation and assembly, the cage will be deformed, as shown in Figure 5. The deformed cage will cause the rollers to get stuck, affecting the rotational flexibility of the bearing. This will cause heat and burns, eventually leading to bearing failure.
After the bearing is installed, it is also very important to adjust the clearance between the outer ring and the inner component. If the clearance is too small, it will cause the temperature to rise too high, accelerate wear and even seize; if the clearance is too large, additional radial runout and axial movement will occur. Movement causes relative displacement between the roller and the outer ring raceway and causes uneven local wear and noise. Only proper adjustment can ensure the normal operation of the bearing.
3. Damage caused by improper use and maintenance
When the bearing is working, if there is insufficient lubricating oil, the direct contact between the metal on the working surface will cause scratches, heat and burns, which will reduce the original hardness of the bearing and cause adhesive wear, eventually leading to bearing failure.
Before the bearing is installed, if the workpiece is not cleaned or the lubricating oil added is not clean (such as mixed with sand, dust, dirt, etc.), or due to unreliable sealing or when working in a dusty environment, some hard particles may enter the bearing roller. The track will cause abrasive wear, and the surface will show fine groove marks or tiny pits, which will increase the clearance of the bearing, reduce the accuracy, and shorten the service life.
If the bearing is subjected to excessive static load or impact load during use, it is likely to cause uneven plastic deformation – indentation – at the contact point between the inner and outer rings and rollers. The occurrence of indentations will increase the vibration and noise of the bearing, increase the temperature, and intensify wear, which will lead to severe spalling and cause the bearing to fail. This situation often occurs in bearings with low speed or swing.
Bearings work in humid media and environments with acid vapor and other substances that cause metal corrosion. If the seal of the bearing is not good, it may cause corrosion. The mixture of rust products and lubricating oil will cause corrosion and wear on the working surfaces of the raceways and rolling elements, and cause surface peeling. If a current passes through the bearing during use, the current may break down the bearing oil film and generate sparks, causing the surface to melt and form small pits or strips.
In order for the bearing to work normally and achieve the expected life, when selecting the bearing, necessary calculations should be made based on the main failure modes of the bearing. For bearings in general operation, the life should be calculated based on contact fatigue failure and rated dynamic load; for high-speed bearings, in addition to life calculation, necessary limit speed verification should be carried out; for bearings with lower speed, static calculation should be carried out. Strength calculation to prevent plastic deformation from occurring. After early failure of a bearing, it is necessary to carefully observe the damage, analyze the cause, and take necessary improvement measures. In addition, the design of the bearing combination structure must be reasonable to ensure sufficient lubrication and reliable sealing, which is very important to increase the service life of the bearing and ensure normal operation.
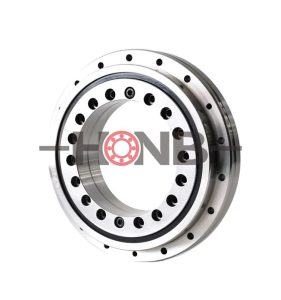
We have rich experience in precision bearing manufacturing and are ranked NO.1 in China and NO.3 all over the world.
We can tailor the overall solution for the use of precision bearings.
HONB– Accountability & Innovation
Products
- YRT rotary table bearing
- YRTS rotary table bearing (high speed series)
- YRTM with integral angular measuring system series
- ZKLDF axial angular contact ball bearing series
- RA series crossed roller bearing
- SX series crossed roller bearing
- CRBH series crossed roller bearing
- RE series crossed roller bearing
- RU series crossed roller bearing
- RB series crossed roller bearing
- XR/JXR series crossed taper roller bearing
- Crossed roller bearing
Contact Us
✉️ bearing20@hyzcgroup.com
📞 +86 15236685001