How to choose grease suitable for bearings
Author: hongyuanTime:
Lubrication is one of the most important considerations for designers. When choosing a lubricant, factors including temperature, load, speed, environment, and life expectancy need to be checked. In addition, many characteristics of greases and lubricants need to be accounted for, such as oil separation, evaporation loss, drop point, oxidation stability, cross-flow capacity/stiffness, etc.
Grease is by far the most commonly used lubricant for radial ball bearings used in motors and gearboxes. Lubricants have low torque characteristics, but are prone to evaporation losses, migration and are not always suitable for lifetime lubrication.
1. Characteristics of grease
As previously stated, greases and lubricants consist of base oils, mineral or synthetic oils, thickeners, and other additives. The properties of standard greases are determined by these components, as well as by the grease manufacturer for proper handling, storage, and good process control of the raw materials.
1.1 Type of base oil
Base oil viscosity is a primary consideration when evaluating potential greases. Viscosity is a measure of “flow”, the flow resistance caused by internal friction between lubricant molecules. This characteristic determines load capacity, film thickness, and operating temperature. The higher the viscosity, the higher the film strength. Viscosity varies with temperature. The higher the temperature, the lower the viscosity. Therefore, it is important to select lubricants based on the operating temperature range. Special high temperature greases, special low temperature greases and greases with very wide temperature ranges can be used to meet specific temperature requirements.
1.2 rigid
Greases are classified according to their consistency or hardness. The American Society for Testing Materials (ASTM) has developed a test method to determine the hardness of grease by placing a cone of specified weight and size into a sample of grease. The cone is removed after 5 seconds and the penetration depth is measured in tenth of a millimetre. The larger the value, the deeper the penetration, the softer the grease. The grease sample is then put into a machine that knocks it (such as baking with a blender or egg beater) to simulate operating conditions. And then try it again. This result is called work penetration and is the basis of classification. The following table lists the National Grease Association (NLGI) classifications.
1.3 thickener
Greases consist of solid soaps such as calcium or lithium soap. In some cases, fine clay is used to form a structure that preserves and disperses the base oil in it. The thickener structure does not provide the actual lubrication, but is a reservoir that releases the lubricant into the contact area.
Although thickeners have little effect on lubrication, they give grease unique properties that affect its applicability in some applications or environments. Among them, lithium and lithium compound thickening grease are the most common.
· Lithium – the most common, easy to manufacture, easy to store, good pumpability, fluidity allows dirt to flow out;
· Calcium – Good water resistance, calcium soap to help lubrication;
· Aluminum – has the highest tolerance to water, chemicals and acids;
· Barium – high water resistance, but certain toxicity;
· Sodium – Fibrous, water soluble.
Another class of thickeners is non-soap thickeners, which are commonly used in applications where high temperatures cause thermal degradation of other types of thickeners. Organic polyurea thickeners provide similar temperature range limitations as metal soaps, but also have antioxidant and wear properties derived from the thickener itself.
· Clay and silica (insoluble powder, silica or clay platelets) – Chemically modified structures and surfaces can be used as gels for greases. The maximum available temperature of these greases is further increased.
· Polyurea – polyurea greases are known as high performance greases because of their extensive performance characteristics.
.jpg)
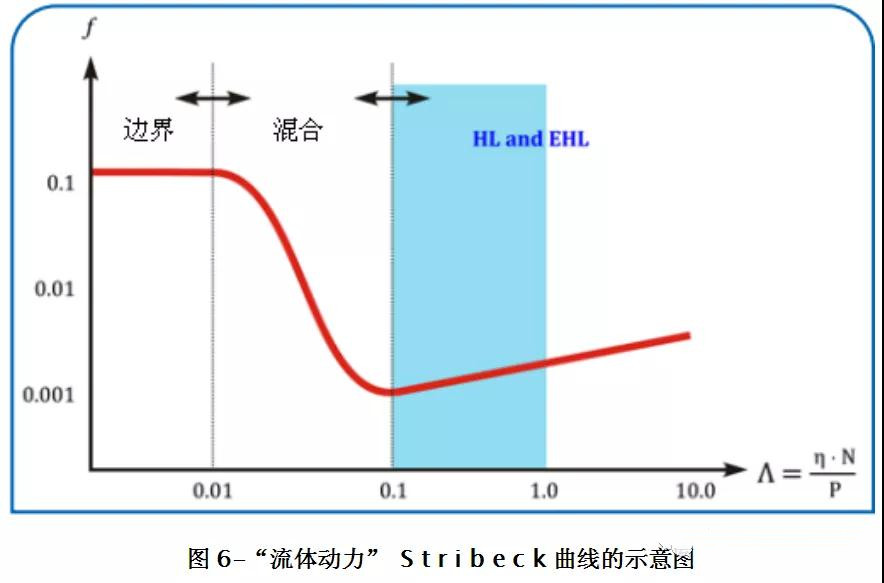
1.4 additive
Additives can strengthen grease. The strengthened greases contain boundary and extreme pressure additives, as well as solid lubricants such as graphite and molybdenum disulfide.
· Corrosion and rust inhibitors — These are very common additives that prevent corrosion and rust of metal parts in contact with lubricants. These additives work by neutralizing acids and forming chemical protective barriers to repel water from the metal’s surface.
· Anti-wear (EP) — Anti-wear additives and/or extreme pressure additives are chemical additives that protect metal surfaces during boundary lubrication. They form a protective film on the worn surface and chemically react with the metal surface to form a sacrificial surface film. They are activated at high loads and high contact temperatures.
· Antioxidants: Most greases and oils contain antioxidants. This extends the life of the base oil. Oxidation can destroy the base oil. Oxidation occurs at any temperature, but accelerates as temperatures rise and in the presence of water, wear metals, and other contaminants.
Viscosity index (VI) : These additives reduce the rate of change of viscosity with temperature.
· Pour point: Pour point additives improve the low temperature working range.
· Tackifier: These additives help the lubricant adhere to the metal surface during rotation.
If you have any questions,pls feel free to contact us.
e-mail:bearing6@hyzcgroup.com
Products
- YRT rotary table bearing
- YRTS rotary table bearing (high speed series)
- YRTM with integral angular measuring system series
- ZKLDF axial angular contact ball bearing series
- RA series crossed roller bearing
- SX series crossed roller bearing
- CRBH series crossed roller bearing
- RE series crossed roller bearing
- RU series crossed roller bearing
- RB series crossed roller bearing
- XR/JXR series crossed taper roller bearing
- Crossed roller bearing
Contact Us
✉️ bearing20@hyzcgroup.com
📞 +86 15236685001