Heat Treatment of High Alloy Die Steel
Author: hongyuanTime:
High-alloy die steels include high-chromium and medium-chromium tool steels, high-speed steels, and matrix steels. This type of steel contains more alloying elements, has the characteristics of good hardenability, high wear resistance and small quenching deformation, and is widely used as a mold with heavy load, large production batch, high wear resistance and complex shape.
(1) High carbon high chromium steel
The composition of this type of steel is characterized by high chromium content and high carbon content, and it is the most widely used and the largest in quantity among cold work die steels. Representative steel grades are Crl2, Crl2MoV, Crl2MolVl (D2), Crl2W, etc.
This kind of steel is usually treated by spheroidizing annealing after forging, and the hardness after annealing is 207~255HB. Commonly used quenching processes are:
1) Quenching at a lower temperature Heat Crl2 steel to 960~980°C, oil-cool, and the hardness after quenching is above 62HRC. For Crl2MoV steel, the quenching temperature is 1020~1050°C, oil cooling, and the hardness after quenching is above 62HRC. Using this method, the steel can obtain high hardness, high wear resistance and high precision size, which can be used to make cold stamping dies.
2) Higher temperature quenching and multiple high temperature tempering For Crl2 steel, heating to 1050~1100℃, oil cooling, the hardness after quenching is 42~50HRC. For Crl2MoV steel, the quenching temperature is 1100~1150℃, oil cooling, and the hardness after quenching is 42~50HRC. Higher temperature quenching plus multiple high temperature tempering can make the steel obtain high red hardness and wear resistance, which can be used to make molds working under high temperature.
Crl2 type steel should be tempered in time after quenching, and the tempering temperature can be determined according to the required hardness. For cold stamping dies that require high hardness, the tempering temperature is between 150 and 170°C, and the hardness after tempering is above 60HRC. For cold stamping dies that require higher strength, hardness and certain toughness, the tempering temperature is 250~270°C, and the hardness after tempering is 58~60HRC. For cold stamping dies that require high impact toughness and a certain hardness, the tempering temperature can be increased to about 450°C, and the hardness after tempering is 55~58HRC. Crl2 steel should avoid the tempering brittle zone of 275~375°C.
(2) High carbon medium chromium steel
There are mainly Cr6WV steel, Cr4W2MoV steel and Cr6MolV steel.
(3) High speed steel
When copper or aluminum parts are cold-extruded, the force on the mold is not too severe, and Crl2 type mold steel can generally be used. However, when ferrous metals are cold-extruded, the force is severe and the working conditions are very harsh, which puts forward higher requirements for the mold. Therefore, it is necessary to use more advanced mold steel, such as high-speed steel, to manufacture molds.
After heat treatment, high-speed steel has high hardness, compressive strength, good wear resistance, and can meet relatively harsh cold extrusion conditions. Commonly used cold-extruded high-speed steels include W6 Mo5 Cr4 V2 steel, Wl8Cr4V steel, and 6W6Mo5Cr4V steel.
Wl8Cr4V steel has good red hardness, and still has high hardness and good toughness at 600°C, but its carbides are coarse, and its strength and toughness decrease with the increase of size. W6Mo5Cr4V2 steel has good red hardness and toughness. After quenching, the surface hardness can reach 64~66HRC. It is a high-speed steel containing Mo and low W. Its carbide particles are relatively fine and evenly distributed, and its strength and toughness are better than Wl8Cr4V steel. .
Most cold extrusion (including cold heading) dies made of high-speed steel can be quenched at a temperature slightly lower than the quenching temperature of high-speed steel tools, such as Wl8Cr4V steel at 1240~1250°C, W6 Mo5 Cr4 V2 steel at 1180~1200°C , and then tempered three times at 560°C. For some slender or thin-walled molds that require high toughness, the quenching temperature can be further reduced to increase their service life. However, after low-temperature quenching, the compressive strength of high-speed steel is reduced, and it cannot be used for high-load molds, and the wear resistance will also be reduced. Table 9.1.3 Hardness and impact toughness of commonly used cold-extruded high-speed steels after quenching and tempering at different temperatures.
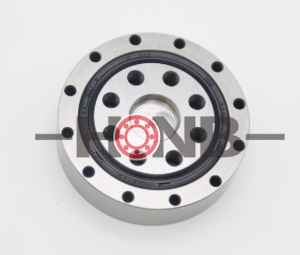
We have rich experience on precision bearing manufacturing and are ranked NO.1 in China and NO.3 all over the world.
We can tailor the overall solution for the use of precision bearings.
HONB– Accountability & Innovation
Products
- YRT rotary table bearing
- YRTS rotary table bearing (high speed series)
- YRTM with integral angular measuring system series
- ZKLDF axial angular contact ball bearing series
- RA series crossed roller bearing
- SX series crossed roller bearing
- CRBH series crossed roller bearing
- RE series crossed roller bearing
- RU series crossed roller bearing
- RB series crossed roller bearing
- XR/JXR series crossed taper roller bearing
- Crossed roller bearing
Contact Us
✉️ bearing20@hyzcgroup.com
📞 +86 15236685001