The friction coefficient of sliding bearings shown in the reference value of stable rotation under general conditions is generally 0.010.020.10.2. The friction coefficient of various types of bearings is the friction coefficient of bearing types. In order to facilitate comparison with sliding bearings, the friction torque of rolling bearings can be calculated according to the bearing inner diameter by the following formula: M=uPd/2 (M: friction torque, mN.m; u: friction coefficient, Table 1; P: bearing load, N; d: bearing nominal inner diameter, mm). The friction coefficient u is greatly affected by the bearing type, bearing load, rotation speed, lubrication method, etc. The reference value of the friction coefficient during stable rotation under general conditions is as follows. For sliding bearings, generally u=0.01-0.02, sometimes up to 0.1-0.2. Composite bearing friction coefficient: 0.03~0.18 Bearing type friction coefficient u Deep groove ball bearing 0.0010-0.0015 Angular contact ball bearing 0.0012-0.0020 Aligning ball bearing 0.0008-0.0012 Cylindrical roller bearing 0.0008-0.0012 Full complement needle roller bearing 0.0025-0.0035 Needle roller bearings with cage 0.0020-0.0030 Tapered roller bearing 0.0017-0.0025 Spherical roller bearing 0.0020-0.0025 Thrust ball bearing 0.0010-0.0015 Thrust spherical roller bearing 0.0020-0.0025 4. Selection of rolling bearing lubrication methods Rolling bearing is an important mechanical component. Whether the performance of a mechanical equipment can be fully exerted depends on whether the bearing is properly lubricated. It can be said that lubrication is a necessary condition to ensure the normal operation of the bearing. It is important for improving the bearing capacity and Service life plays an important role. No matter what form of lubrication is used, lubrication can play the following roles in rolling bearings: (1) Reduce friction between metals and slow down their wear. (2) The formation of oil film increases the contact area and reduces contact stress. (3) Ensure that the rolling bearing can operate normally for a long time under high-frequency contact stress and extend the fatigue life. (4) Eliminate frictional heat, reduce the temperature of the bearing working surface, and prevent burns. (5) It has the functions of preventing dust, rust and corrosion. Therefore, correct lubrication is very important for the normal operation of rolling bearings. The lubrication design of rolling bearings mainly includes: determination of reasonable lubrication methods, correct selection of lubricants, quantitative calculation of lubricant dosage and determination of oil change intervals. Rolling bearing lubrication can generally be divided into three categories: oil lubrication, grease lubrication and solid lubrication according to the type of lubricant used. Among them, oil lubrication has a wider temperature range than other lubrication methods, and is more suitable for bearings working under high-speed and high-load conditions. At the same time, oil lubrication also has the advantages of convenient equipment maintenance and lubricant replacement, and friction pairs in the system such as gears, etc. It has the advantage of being lubricated at the same time, so so far, the use of oil lubrication for bearings is the most common. Grease lubrication has the advantages of simple sealing device, low maintenance cost and low grease cost. It is widely used in bearings operating at low speed, medium speed and medium temperature. In particular, the advent of anti-wear additives in recent years has improved the lubrication performance of grease and made grease lubrication more widely used. If oil lubrication and grease lubrication cannot meet the lubrication conditions required by the bearing, or cannot meet specific working conditions, you can use solid lubricants or try to improve the lubrication performance of the bearing itself. The rotation speed of the bearing is mainly limited by the temperature rise caused by the friction and heat inside the bearing. When the rotation speed exceeds a certain limit, the bearing will be unable to continue rotating due to burns, etc. The limiting speed of a bearing refers to the limit value at which it can rotate continuously without generating frictional heat that may cause burns. Therefore, the limiting speed of the bearing depends on various factors such as the type, size and accuracy of the bearing, the lubrication method, the quality and quantity of the lubricant, the material and type of the cage, and the load conditions. The limiting speeds of various types of bearings using grease lubrication and oil lubrication (oil bath lubrication) are listed in each bearing size table. The values represent the standard design bearings under normal load conditions (C/P>=13, Fa/Fr<= The limit value of the rotation speed when rotating at about 0.25).
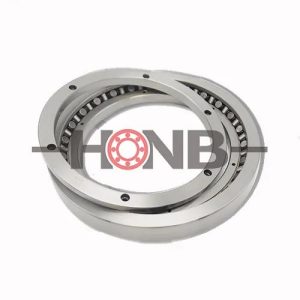
We have rich experience in precision bearing manufacturing and are ranked NO.1 in China and NO.3 all over the world.
We can tailor the overall solution for the use of precision bearings.
HONB– Accountability & Innovation
- YRT rotary table bearing
- YRTS rotary table bearing (high speed series)
- YRTM with integral angular measuring system series
- ZKLDF axial angular contact ball bearing series
- RA series crossed roller bearing
- SX series crossed roller bearing
- CRBH series crossed roller bearing
- RE series crossed roller bearing
- RU series crossed roller bearing
- RB series crossed roller bearing
- XR/JXR series crossed taper roller bearing
- Crossed roller bearing
✉️ bearing20@hyzcgroup.com
📞 +86 15236685001