Crossed roller bearing machining cooling process
Author: hongyuanTime:
The reason why crossed roller bearings have an irreplaceable role in machinery and equipment, which is not only related to his structural characteristics, but also with his production and processing of the thousands of hammering has a certain relationship.
A. Multi-process processing
Crossed roller bearing parts require high, the production process must be more. General bearing production requires 20 to 40 processes, as many as 70 more.
Second, forming processing
The working surface of bearing parts are rotary forming surface, suitable for processing with forming method. Such as the ring raceway forging rolling and grinding, are used to form the tool or anti-shape plate processing.
Third, precision machining
The majority of the surface of the crossed roller bearing parts to be ground, grinding size and geometric accuracy are in μM, especially the raceway of the ring and rolling body of higher precision, need super finishing or grinding processing.
1, annealing cooling mode: steel annealing, generally used with the furnace cooling to 600 ~ 550 ℃ below and then out of the furnace air cooling.
2, normalizing cooling mode: steel normalizing, generally used in the air cooling.
3, quenching cooling mode: steel quenching, steel in the most unstable range of supercooled austenite (650 ~ 550 ℃) cooling rate should be greater than the critical cooling rate, so as to ensure that the workpiece does not transform into pearlite type organization; and the cooling rate near the Ms point should be as low as possible, so as to reduce the quenching stress, reduce the workpiece deformation and cracking. Therefore, quenching, in addition to the selection of suitable quenching cooling medium, should also improve the quenching method. Simple shape of the workpiece, often using simple single-liquid quenching method, such as carbon steel with water or brine liquid as a cooling medium, alloy steel commonly used as a cooling medium oil.
4, tempering cooling method: carbon steel tempering, generally used in the air cooling.
Normalizing process is a heat treatment process of heating the steel parts to 30 to 50 ℃ above Ac3, after holding the appropriate time, cooling in still air. The normalization of steel parts heated to more than 100 ~ 150 ℃ above Ac3 is called high-temperature normalization. For low carbon steel castings, forgings, the main purpose of normalizing is to refine the organization. Compared with annealing, after normalizing the pearlite layer is fine, ferrite grains are also relatively small, thus higher strength and hardness. Low-carbon steel due to annealing hardness is too low, cutting and machining the phenomenon of sticky tool, cutting performance is poor, through the normalization to increase hardness, can improve cutting performance, some medium carbon structural steel parts can be normalized instead of tempering, simplify the heat treatment process.
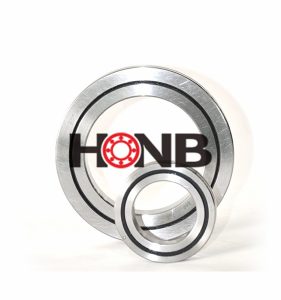
Previous Page:Influence of bearing preload method and speed
Next Page:How to maintain the roller bearings?
Products
- YRT rotary table bearing
- YRTS rotary table bearing (high speed series)
- YRTM with integral angular measuring system series
- ZKLDF axial angular contact ball bearing series
- RA series crossed roller bearing
- SX series crossed roller bearing
- CRBH series crossed roller bearing
- RE series crossed roller bearing
- RU series crossed roller bearing
- RB series crossed roller bearing
- XR/JXR series crossed taper roller bearing
- Crossed roller bearing
Contact Us
✉️ bearing20@hyzcgroup.com
📞 +86 15236685001