Needle roller bearings are roller bearings with cylindrical rollers. They are commonly seen in cars or motorcycles in our daily lives. Needle roller bearings cannot avoid some failures during use. According to our understanding of needle roller bearings , tell you about some common failure factors of needle roller bearings, and related methods to eliminate bearing failures. Common faults of needle roller bearings and their causes: 1. Failure form: (1) The bearing has difficulty rotating and generates heat; (2) The bearing makes abnormal noise when running; (3) The bearing generates vibration; (4) The inner race is peeled off and cracked; (5) The outer seat ring peels off and cracks; (6) Indentations are produced on the bearing raceways and rolling elements. 2. Failure cause analysis: (1) Inspection before assembly is not careful. Before assembling the bearing, clean and carefully check the inner and outer races, rolling elements and cages of the bearing to see if there is rust, burrs, bruises and cracks; check whether the bearing clearance is appropriate. Whether the rotation is brisk and free, and whether there is any sudden jamming. phenomenon; at the same time, check the size, roundness and cylindricity of the shaft diameter and bearing seat hole, as well as whether there are burrs or uneven convexities on the surface. For split bearing seats, it is required that a gap of 0.1mm~0.25mm should be left between the joint surface of the bearing cover and the bearing base and the outer circular surface of the outer seat to prevent “clamping” at the “tile openings” on both sides of the outer seat. The gap caused by “helping” phenomenon is reduced and wear is accelerated, causing premature bearing damage. (2) Improper assembly. Improper assembly will cause the bearings to have the various failure modes mentioned above, as well as the following situations: A. Improper cooperation: The fit between the inner hole of the bearing and the shaft adopts the base hole system, and the fit between the outer circle of the bearing and the bearing seat hole adopts the base shaft system. Generally, the shafts and bearing inner races of centrifugal pumps, centrifuges, reducers, electric motors and centrifugal compressors that work under normal load conditions use J5, js5, js6, k5, k6, m6, and the bearing seat hole and bearing The outer race uses j6 and J7 fit. The rotating seat ring (the inner seat ring of most bearings is a rotating seat ring, the outer seat ring is not a rotating seat ring, and a small number of bearings are the opposite), usually using an interference fit, which can prevent the seat ring from being in the shaft diameter under load. Rolling and sliding occur on the mating surface of the bearing housing bore. However, sometimes due to inaccurate measurement of the shaft diameter and bearing seat hole or the roughness of the mating surface not meeting the standard requirements, an excessive interference fit is caused, which causes the bearing seat ring to be greatly squeezed, resulting in radial clearance of the bearing itself. Reduction will make the bearing difficult to rotate, generate heat, intensify wear or get stuck. In severe cases, it will cause the inner and outer races of the bearing to crack during installation. The non-rotating seat ring often adopts a fit with small clearance or interference. In this way, the non-rotating seat ring may cause slight crawling, causing the contact surface between the seat ring and the rolling element to be constantly replaced, and the raceway of the seat ring to wear evenly. At the same time, it can also eliminate the axial jamming of the rolling elements in the bearing due to thermal elongation of the shaft. However, an excessive clearance fit will cause the non-rotating seat ring to rotate together with the rolling elements, causing serious wear between the shaft (or bearing seat hole) and the inner seat ring (or outer seat ring), and friction will cause the bearing to heat up and vibrate. B. Improper assembly method: When the interference between the bearing and the shaft diameter or the bearing seat hole is small, the press-in method is often used for assembly. The simplest method is to use a copper rod and a hand hammer to symmetrically tap the interference fit seat ring of the bearing in a certain order to make the bearing press in smoothly. In addition, a soft metal casing can also be driven in with a hand hammer or pressed in with a press. Improper operation will cause the seat ring to deform and crack, or hammering the seat ring with a non-interference fit will cause indentations on the raceways and rolling elements or the bearing will be indirectly damaged. C. Improper temperature control during assembly: When assembling needle roller bearings, if the interference with the shaft diameter is large, the hot assembly method is generally used. That is, the bearing is placed into an oil drum containing oil, and the outside of the oil drum is heated with hot water or flame. The process requires that the heated oil temperature be controlled at 80°C ~ 90°C, generally not exceeding 100°C, and not exceeding 120°C at most. After the bearing is heated, it is quickly taken out and set on the journal. If the heating temperature is too high due to improper temperature control, the bearing will temper and reduce its hardness. The bearing will be prone to wear, peeling, or even cracking during operation. D. Improper gap adjustment during assembly: The clearance of needle roller bearings is divided into radial clearance and axial clearance. Its function is to ensure the normal operation and lubrication of the rolling elements and to compensate for thermal elongation. For bearings with adjustable clearance, there is a proportional relationship between the axial clearance and the radial clearance, so the installation requires only adjusting the axial clearance to obtain the required radial clearance, and they are generally They are used in pairs (that is, installed at both ends or one end of the shaft), so only the axial clearance of one bearing needs to be adjusted. Generally, gaskets are used to adjust the axial clearance, and some can also be adjusted with screws or thrust blocks. For needle roller bearings whose clearance cannot be adjusted, the radial clearance has been determined according to the standard during manufacturing and cannot be adjusted. After such bearings are installed on the shaft diameter or in the bearing seat hole, the actual radial clearance is called In order to assemble the radial clearance, the size of the assembly radial clearance should be just enough to create the necessary working radial clearance during operation to ensure that the bearing rotates flexibly. When this type of bearing is working, the shaft is heated and elongated when the temperature rises, causing the relative displacement of the inner race, thereby reducing the radial clearance of the bearing, and even causing the rolling elements to get stuck between the inner and outer races. If an axial clearance is left between one bearing of the double-supported needle roller bearing (the other bearing is fixed on the shaft and in the bearing seat) and the side cover, the above phenomenon can be avoided. From the above, it can be seen that regardless of the needle roller bearings with adjustable or non-adjustable clearance, they must adjust the axial clearance during assembly (but some bearings with non-adjustable clearance do not need to leave axial clearance) to compensate for the increase in shaft temperature. The thermal elongation of the rolling element ensures the normal operation of the rolling element. If the axial clearance is too small, it will cause the bearing to rotate difficultly, generate heat, and even cause the rolling elements to become stuck or damaged; if the axial clearance is too large, it will cause abnormal noise during operation, and even cause severe vibration or damage to the cage. . E. Improper coupling alignment: The input shaft of most operating equipment is connected to the power shaft through a coupling. Therefore, the coupling must be aligned during assembly so that the driving shaft and the driven shaft are on the same axis. (3) Poor lubrication. The lubricating oil (or grease) used in needle roller bearings has a certain operating temperature. When the temperature is too high, it will deteriorate and lose its lubrication effect, causing the bearing to burn due to high temperature. In addition, if the quality of the lubricating oil (or grease) itself is poor or the oil (grease) is not added in time during operation, it will also cause the bearing temperature to rise or produce abnormal noise. (4) The rotor is unbalanced. Generally speaking, the rotor of the operating equipment must be dynamically and statically balanced before assembly, so there will be no problems with the bearings. However, during operation, some rotors are corroded by media or worn by solid impurities, or the shaft is bent, which will cause unbalanced centrifugal force, causing the bearings to heat and vibrate, and the raceways to be severely worn until they are destroyed. (5) Inspection and replacement are not timely. During the operation of the bearing, check it regularly according to regulations. If there is heat, abnormal sound, vibration, etc., stop the machine in time to find the cause and eliminate the fault. If the bearing is found to have severe fatigue spalling, oxidation rust, wear pits, cracks, hardness, etc. When the HRC is reduced to <60, or there is too much noise that cannot be adjusted, it should be replaced in time. If the inspection and replacement are not timely, it will cause serious damage to the bearings and even the rotor, thus affecting normal production. In addition, vibration caused by improper bearing disassembly and loose equipment anchor bolts will also cause indentations on the bearing raceways and rolling elements, and cracks in the inner and outer races of the bearing. Methods to eliminate needle bearing failures: (1) When replacing a bearing, carefully inspect the new bearing, as well as the shaft diameter, bearing seat hole and rotor; (2) When assembling and disassembling bearings, strictly implement the maintenance process and operate carefully to avoid bearing damage caused by improper assembly and disassembly; (3) Refuel and change oil on time to ensure that the bearing is always in good condition; (4) Check carefully during operation to find potential faults and eliminate them in time.
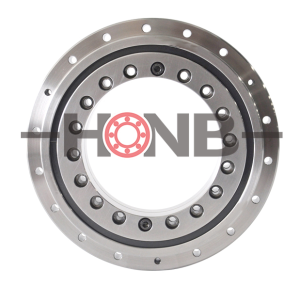
We have rich experience in precision bearing manufacturing and are ranked NO.1 in China and NO.3 all over the world.
We can tailor the overall solution for the use of precision bearings.
HONB– Accountability & Innovation
- YRT rotary table bearing
- YRTS rotary table bearing (high speed series)
- YRTM with integral angular measuring system series
- ZKLDF axial angular contact ball bearing series
- RA series crossed roller bearing
- SX series crossed roller bearing
- CRBH series crossed roller bearing
- RE series crossed roller bearing
- RU series crossed roller bearing
- RB series crossed roller bearing
- XR/JXR series crossed taper roller bearing
- Crossed roller bearing
✉️ bearing20@hyzcgroup.com
📞 +86 15236685001