Home > News > Product Knowledge > Common failures of hydrostatic bearings and the causes of failure and elimination methods
Common failures of hydrostatic bearings and the causes of failure and elimination methods
Author: hongyuanTime:
Hydrostatic bearings in the process of use, often encounter some bearing failure phenomenon, today for the common failure of hydrostatic bearings and the causes of failure and elimination methods are organized, I hope it will help you.
Hydrostatic bearing
Hydrostatic bearing failure one: pure liquid lubrication can not be established
Failure phenomenon: automatic oil pump, if the establishment of pure liquid lubrication, generally should be able to easily rotate by hand; if not turn or more difficult to turn than when not supplying oil, that indicates that the pure liquid lubrication is not established.
Failure causes: bearing a certain oil cavity pressure failed to establish, or bearing assembly quality is too poor, such as.
(1) an oil cavity with oil leakage, resulting in the shaft is squeezed in the side of the bearing.
(2) a bearing oil cavity without lubricant, processing and assembly of the oil inlet holes have misalignment, or throttle is blocked.
(3) The difference between the liquid resistance of each throttle is too large, resulting in an oil cavity without bearing capacity.
(4) Feedback throttle elastic element stiffness is too low, resulting in one end of the oil hole is blocked.
(5) The coaxiality of the radial bearing is too large, or the verticality of the thrust bearing is too small, so that the lifting clearance of the spindle is too small.
Elimination method.
(1) Check whether the pressure of each oil cavity has been established. For oil leakage or no pressure oil cavity, find out the specific reason and take corresponding measures to overcome.
(2) Adjust the throttling ratio of each oil cavity so that it is within a reasonable range.
(3) Design the throttle reasonably.
(4) Keep the lubricating oil clean.
(5) Ensure the manufacturing accuracy and assembly quality of the parts.
Hydrostatic bearing failure II, unstable pressure
Failure phenomenon.
(1) when the spindle does not turn, after the oil pump is turned on, the pressure of each oil cavity gradually decreases or the pressure of a few oil cavities decreases.
(2) After the spindle rotates, the pressure of each oil cavity has periodic changes (if the change is greater than 0.05~0.1MPa, the cause must be checked).
(3) When the spindle is not rotating, each oil cavity is jittering due to pressure (if the change is more than 0.05~0.1MPa, it should be checked).
(4) When the spindle speed is high, the oil cavity pressure has irregular fluctuations.
Cause of failure.
(1) Poor throttle ratio β value.
(2)The oil supply pressure p. is too low.
(3) bearing clearance is too large.
(4) Throttle design is not reasonable.
Elimination methods.
(1) replace the oil, clean the oil filter and throttle.
(2) check whether there is a large centrifugal force on the shaft and shaft parts, if so, check the dynamic balance to eliminate the unloading belt to check whether there is interference, reduce the coaxiality error between the unloading belt pulley and the spindle.
(3) Check the oil pump and pressure valve.
(4) Improve the type of oil chamber.
Ensure Re>2000.
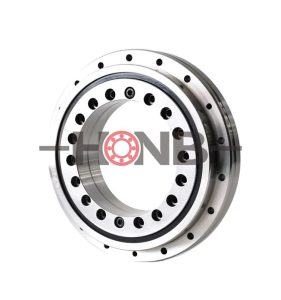
We have rich experience on precision bearing manufacturing and are ranked NO.1 in China and NO.3 all over the world.
We can tailor the overall solution for the use of precision bearings.
HONB– Accountability & Innovation
Previous Page:Types and functions of oil seals
Products
- YRT rotary table bearing
- YRTS rotary table bearing (high speed series)
- YRTM with integral angular measuring system series
- ZKLDF axial angular contact ball bearing series
- RA series crossed roller bearing
- SX series crossed roller bearing
- CRBH series crossed roller bearing
- RE series crossed roller bearing
- RU series crossed roller bearing
- RB series crossed roller bearing
- XR/JXR series crossed taper roller bearing
- Crossed roller bearing
Contact Us
✉️ bearing20@hyzcgroup.com
📞 +86 15236685001