Bearing ring precision cold rolling technology
Author: hongyuanTime:
Precision cold rolling technology is a cold forming method that extrudes and plastically deforms annular rotating parts at room temperature to obtain finished parts. Precision cold rolling can make the size and shape of the workpiece as close as possible to the theoretical value of the finished part. The advantages are:
1. Can significantly improve material utilization and processing efficiency. Compared with traditional turning processing, precision cold rolling processing can increase the material saving rate by more than 10% to 15%, thereby realizing the cutting processing of bearing rings and reducing processing costs.
2. Can improve the quality of finished products. Due to the rolling method, the metal streamlines inside the parts are continuous and complete, the metal grains are uniform and small, and the structure is dense, so the strength of the parts is improved. At the same time, due to the existence of residual surface stress in the finished parts, the deformation of the parts after heat treatment is also small.
3. It can save energy and improve the working environment. Compared with forging dies, the equipment required for precision rolling is smaller, which can significantly reduce the noise during processing and has obvious energy saving effects. Compared with turning billet making, the noise and dust are smaller.
When rolling the workpiece, the rolling wheel drives the workpiece to rotate, and the core roller squeezes the workpiece under the push of the support wheel that is firmly connected to the feeding device, thereby achieving rolling of the workpiece. From the perspective of the stress condition of the workpiece, the conditions for forming are as follows: the force in the horizontal direction of the workpiece must be balanced with the force exerted in the feed direction, which is a necessary condition for stable deformation; the force in the vertical direction of the workpiece must be greater than or equal to The pushing force generated by the deformation of the workpiece is the condition for the rolling to continue. The above two forces are the components of the normal force in the horizontal and vertical directions of the arc of contact between the support wheel or core roller and the workpiece. The deformation is effective when the feed amount of the support wheel is enough to ensure that the plastic deformation covers the entire wall thickness of the workpiece. Moreover, the feed amount depends on the driving power of the roller, the thrust of the support wheel, and the curvature radius of the roller and core roller. The size of the feed determines the length of the contact arc between the support wheel or core roller and the workpiece, which corresponds to the normal deformation force generated by the deformation of the workpiece. The longer the contact arc, the greater the deformation force.
Due to the different curvature radii of the inner and outer circles of the rolling wheel, core roller and workpiece, the deformation produced by each feed on the inside and outside of the workpiece is unequal. The deformation produced on the outer circle of the workpiece is greater than the deformation of the inner circle. As the rolling process proceeds, the difference in deformation of the inner and outer circles will decrease. Roundness stick is used to control the cylindricity of the workpiece. During the rolling process of the workpiece, the roundness rod is always close to the outer circle of the workpiece, retreats as the outer diameter of the workpiece increases, and provides a constant full circle bending moment. The use of roundness rods can also ensure the stability of the workpiece rolling process and effectively reduce vibration during rolling, thereby extending the life of the mold and machine tool spindle bearings.
At present, foreign precision rolling equipment mainly includes the URAW series of Germany’s BAD DUBEN and the CRF and TCR series of Japan’s KYOEI. They respectively represent two technical routes: BAD DUBEN uses vertical layout and electro-hydraulic position servo control system to improve the rolling accuracy, while KYOEI uses a horizontal layout, rough rolling and a combination of workpiece diameter to improve the rolling accuracy of the workpiece. Dimensional accuracy.
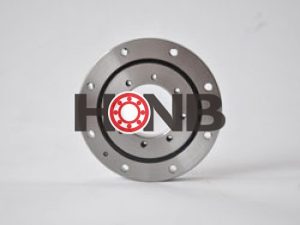
We have rich experience in precision bearing manufacturing and are ranked NO.1 in China and NO.3 all over the world.
We can tailor the overall solution for the use of precision bearings.
HONB– Accountability & Innovation
Next Page:Nylon cage usage analysis
Products
- YRT rotary table bearing
- YRTS rotary table bearing (high speed series)
- YRTM with integral angular measuring system series
- ZKLDF axial angular contact ball bearing series
- RA series crossed roller bearing
- SX series crossed roller bearing
- CRBH series crossed roller bearing
- RE series crossed roller bearing
- RU series crossed roller bearing
- RB series crossed roller bearing
- XR/JXR series crossed taper roller bearing
- Crossed roller bearing
Contact Us
✉️ bearing20@hyzcgroup.com
📞 +86 15236685001